As the use of stainless steel is (and has) increased significantly over the years, the fabrication industry has kept pace with a variety of welding processes, each with benefits and drawbacks that must be evaluated to select the best method of joining. With such a wide variety of base metals and applications in the market, one can choose a welding process that will give the best combination of quality, speed, and eventually, overall cost.
By Fred Schweighardt, Director of Business Development, Advanced Fabrication Markets, Airgas
Stainless steel use in industrial applications spans a wide range of alloys and thicknesses. These are two important initial parameters to be considered when selecting the welding process. Not every base metal alloy is readily welded by every process. Equally, not every welding process is suited for all metal thicknesses. This article will investigate some of the characteristics of the main processes used in industry, with an emphasis on pros, cons, costs, and special considerations.
Shielded Metal Arc Welding – SMAW or ‘Stick’
This process is rarely chosen for production operations, but can be very convenient for remote or very small maintenance and repair jobs. The electrical current travels through the flux-covered electrode and melts the core wire, which deposits the desired weld. A good range of alloys are available, including the very common 308, 309, and 316 alloys, as well as the higher alloy 310, 312, and duplex materials. One of the key details about the specification of these electrodes is the suffix of -15, -16, -17 or -26. These suffixes identify appropriate polarity and usability, with the -15 used with DCEP and in all positions, the -16 and -17 used on DCEP or AC current in all positions, and the -26 used with either DCEP or AC, and is to be used in the flat and horizontal position only.
The SMAW process is suitable for material thicknesses of ~3/16” to essentially unlimited. There is no required externally supplied shielding gas, making the process more portable and convenient.
The power supply is relatively inexpensive, and a welder with a carbon steel SMAW experience will be able to use this process immediately. There is, however, the drawback of the slag residue, which must be well-cleaned, and the relative inefficiency of the process as related to the pounds of weld metal deposited per hour.
Gas Tungsten Arc Welding – GTAW or ‘TIG’
This is a very common process for joining stainless steel, as it allows the user to independently control the electrical energy and the addition of filler metal for a tremendous array of alloys. GTAW is often used when a higher quality weld deposit is required, such as in the process piping industry. This is a gas shielded process, necessary to prevent atmospheric contamination of the weld. Most often, pure argon is chosen as the shielding gas, with occasional use of argon/helium or argon hydrogen mixes.
Virtually all base metals can be successfully welded, with a very large variety of filler metals available, possibly more than any other welding process. Important process limitations are the deposition rate, which can be as low as one pound of filler metal per hour. The travel speed is quite low, which dramatically increases the heat input, bringing about a number of issues in sensitive alloys. Properly developed welding procedures are critical for this process. The advantages of the ‘TIG’ process are: compatibility with the broadest range of base metals, potential for very high quality welds, and a material thickness range from foil to unlimited.
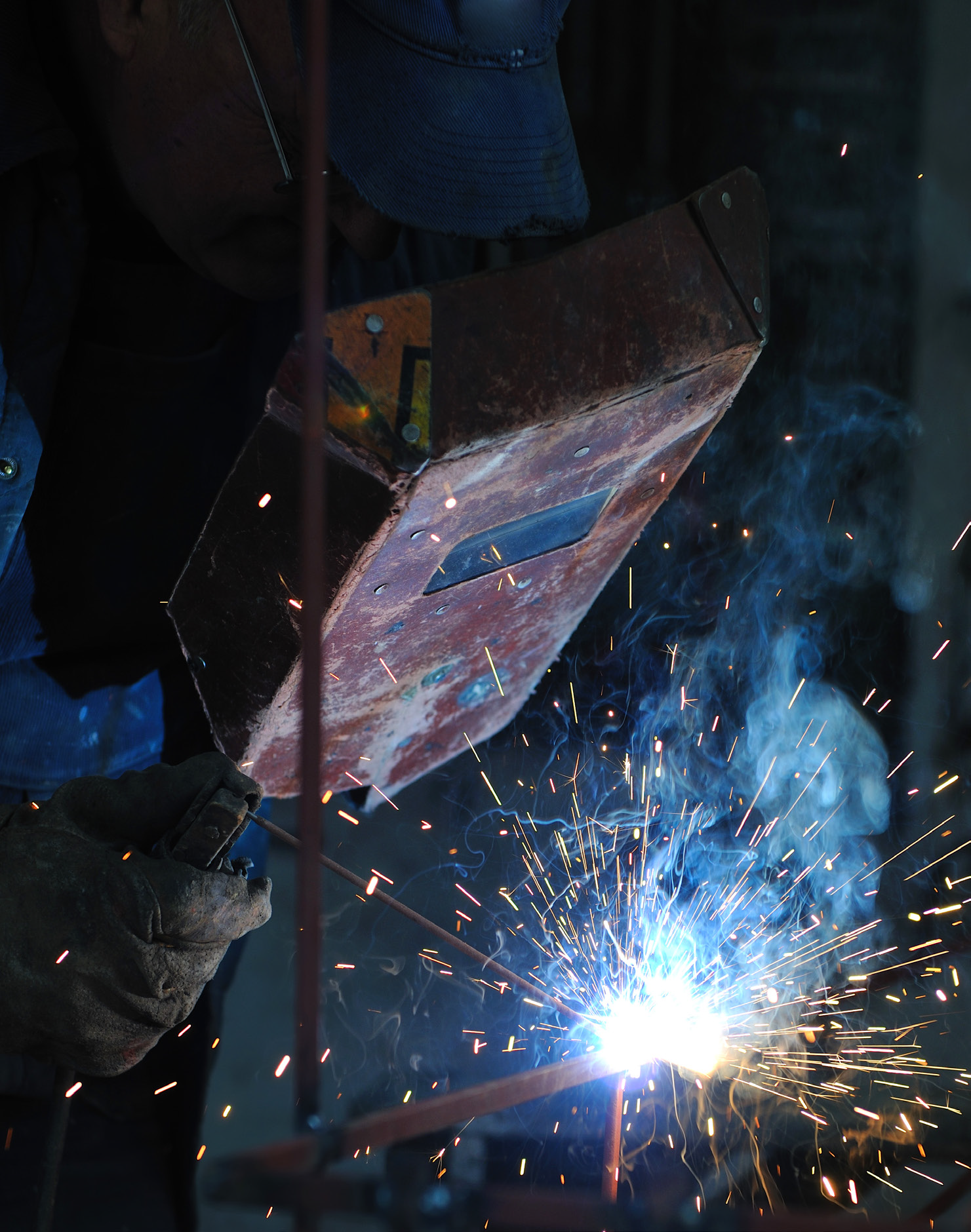
Gas Metal Arc Welding – GMAW or ‘MIG’
The GMAW process is very common in the stainless steel fabrication market, as it has excellent thickness range capability, good alloy availability, and the potential for high productivity. A solid stainless steel filler wire carries current and is melted off into the weld joint. Shielding gas must be used to protect the molten metal and wire. Deposition rate ranges between three and 12 (or more) pounds per hour. The shielding gas selected and power levels determine the rate of melt-off, as well as the applicability of the process to different thicknesses.
Thin-gauge material is generally welded at the lower end, with heavy applications able to withstand the higher heat and penetration of the high-deposition processes. Care must be taken with the process to prevent lack of fusion and penetration at low levels of operation. Shielding gas is always necessary, and it is generally an argon-rich gas, with additions of helium or CO2. Some mixtures use a major component of 90% helium, but this mix is very expensive and can be difficult to source. The equipment used for this process can range from fairly inexpensive to full-features power supplies capable of advanced process control. These advanced systems can often benefit the user by allowing the use of a lower-cost shielding gas, and providing heat input control.
Flux Cored Arc Welding – FCAW or ‘Flux-Core’
This process is a variation of GMAW, but in this case, the continuous solid wire is replaced with a tubular wire that contains various shielding and slag forming components. Often, there is also a shielding gas used, but not always. In general, the dual-shielded welds have a better surface appearance, and the slag covering developed from the flux removes quite easily. The FCAW process is suited for medium to thick material, and is the best process for high deposition rates for the vertical or overhead positions. Pipe welds, in particular, are often finished out with FCAW in the small to medium sizes.
One of the considerations with stainless steel FCAW is the positional designation of the wire. The wire designation will contain the alloy description and a capital letter ‘T’, followed by a ‘1’ or ‘0’. The ‘1’ indicates usability in all positions, and the ‘0’ is for flat and horizontal fillets. There is a significant potential for lack of fusion at the root of a fillet weld in the flat and horizontal positions if lower-end parameters are used. Typically, the same equipment that is used for MIG can be used for FCAW. Most common alloys are available with FCAW consumables, including 308, 309, and 316, as well as several duplex materials.
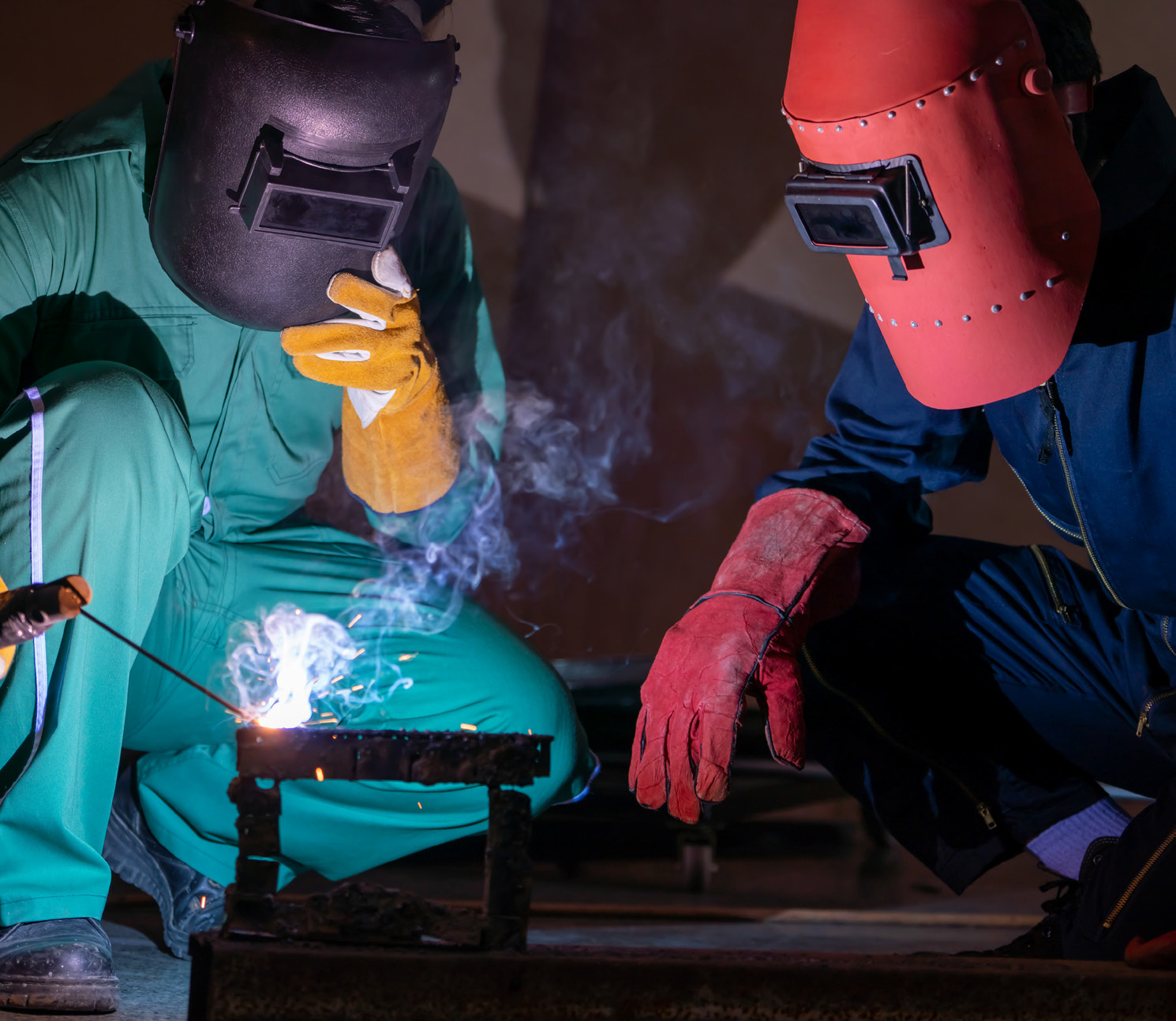
Submerged Arc Welding – SAW or ‘Sub-Arc’
The submerged arc welding process uses a current carrying wire and a special granular flux that serves to protect the weld metal from the atmosphere, and can also modify the alloying activity in the weld pool. The stainless steel wire is located near the plate, and then a hopper covers the arc area with the flux. As the arc is struck and welding is started, the wire and flux are moved along the weld seam together, keeping the weld pool under the covering flux.
As with SMAW, there is no need for any externally supplied shielding gas. The process generally uses larger wires and higher currents than some of the gas shielded methods, and as a result, is mainly used on heavier material in the flat position where a large amount of weld metal is needed. The process is almost always automated, with travel, electrical parameters, and wire speed all coordinated to generate the desired weld.
Choosing the Best Method
While there are many other welding processes that can be used for stainless steel, the above represent more than 90% of the market. Consideration of the various pros and cons of the processes, in addition to their thickness and deposition rate capabilities will provide the user with guidance on the most cost effective method. Deposition rate is particularly important, as that is the parameter that defines the total weld time, and with the understanding that ~80% of the cost of a weld is labor (and time) cost, one can accurately estimate the cost per foot of weld.
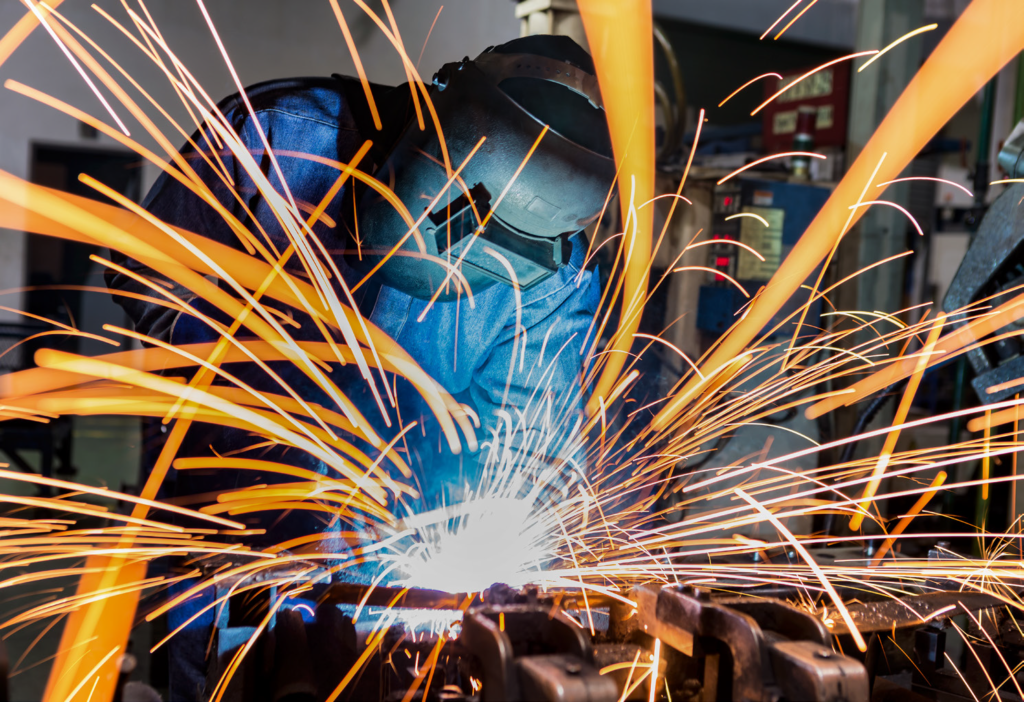
For example, consider a foot of ⅜” fillet weld. This weld weighs .280 pounds, in a realistic 15% overweld/reinforcement condition. With the GMAW process selected, running a .035” wire at 400 IPM, versus the GTAW process, consuming ⅛” wire at 15 IPM, it can be established that the GMAW or MIG process will deposit metal at about 6.5 pounds per hour, and the GTAW or TIG process will put down about 3 pounds per hour. At a fully burdened labor cost of around USD $45 per hour, that means that every foot of this kind of weld will cost about USD $97 more to make with the GTAW process, rather than the GMAW process. Of course, this pre-supposes that the weld is made in the flat position — if it was in the vertical-up orientation, the GMAW process would not work well at the given parameters. To conclude, careful consideration of the variables involved in production will allow for the most cost-effective solution.
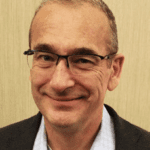