When dealing with corrosion it is important to remember that there is not a ‘one-size-fits-all’ solution. There may be a multitude of factors that result in the corrosion of a material or piece of equipment. Proper monitoring and inspection are therefore essential to ensuring the structural integrity of an application, as is the ongoing presence and advice from knowledgeable corrosion engineers.
Stainless Steel World Americas had the pleasure of speaking with Yushu Wang, a Materials and Corrosion Engineer at PEMEX Deer Park Refinery about his dynamic career. Wang was able to shed light on how he got his start in corrosion engineering, the key components of assessing material integrity, and stainless steel preservation.
By Angelica Pajkovic
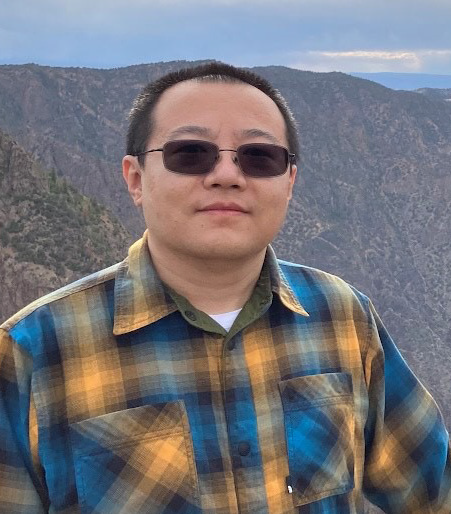
Career in Corrosion
In 2015, Wang graduated from The Georgia Institute of Technology with a Ph.D in Materials Science and Engineering. His thesis was on the pitting corrosion of stainless steels. Following his graduation, he began his career as a Materials and Corrosion Engineer in Shell Global Solutions. In addition to performing focused asset integrity reviews on offshore platforms, Wang acted as the technical lead for several failure analyses and corrosion testing program for the asset support team in Shell P&T. To gain field experience, Wang joined the Pressure Equipment Integrity department as a Materials and Corrosion Engineer at Deer Park Refinery in 2017 (Shell at the time, PEMEX since 2022). He has provided site-wide support for run and maintain activities, projects, and turnaround as a Materials and Corrosion technical authority.
While his role entails numerous day-to-day responsibilities, Wang’s priority as a Materials and Corrosion Engineer, is overseeing five primary components of materials and corrosion management: material selection, monitoring, inspection strategies, abnormal situation management, and failure analysis.
Five Key Responsibilities
Material Selection
The first and foremost way to mitigate the risk of corrosion is through proper design and material selection. Carbon steel is the cheapest and most popular material of selection in many applications. However, it corrodes readily when exposed to most process environments. Therefore, the use of carbon steel should be complemented with good inspection plan.
In cases where the corrosion rate becomes unmanageable, coating can be applied as a barrier between carbon steel and the process to prevent corrosion. A coating that is compatible with the process environment should be selected. However, coating is not always a reliable solution to corrosive environment. Poor coating application can lead to premature failures of the equipment. Attention needs to be paid to the coating condition during the service life of the equipment as well. Since most coatings are expected to last from 10 to 20 years, monitoring of coating condition and proper maintenance of the coating are crucial as well.
In other cases, the use of the corrosion resistant alloys eliminates damage mechanisms that applies to carbon steel. Different materials are often considered based on the intended application and the environment it is exposed to. The two most frequently used materials for refining processes, are stainless steel and carbon steel. “While stainless steels are reliable materials that can withstand a variety of changes in its environments, they are susceptible to chloride pitting, chloride stress corrosion cracking,” explained Wang. Having the correct process conditions is also pivotal in material selection. “For example, while 304 and 316 stainless steels are resistant to sulfuric acid corrosion when concentration is very low (< 5%) or very high (> 93%) at ambient temperature, they should not be selected when sulfuric acid concentration is between 10% to 90%.” As part of his role is to support material selection, Wang works closely with the process and project engineers to select materials that help managing process safety risks economically.
Monitoring
Integrity Operating Windows (IOWs) are essentially ranges of process parameters within which integrity of the equipment can be preserved. Operating within IOWs ensures no excessive corrosion or fast acting damage mechanisms on process equipment. As a materials and corrosion engineer, he responds to critical IOW exceedances, reviews standard IOW exceedances, and performs long term proactive monitoring monthly to assess the system health based on trends of process parameters that have IOW information limits.

Inspection Strategies
One of the most important aspects of Wang’s role is performing risk based inspection (RBI) assessment and set up inspection strategy. He works together with his inspectors to determine how frequently an inspection should be planned and where the focus of the inspection should be. RBI methodology is based on the probability and consequence of a potential failure. “If the probability and consequence of failure is high, it should probably be designed out, or at the least inspected frequently. If the probability and consequence of failure are low, we do not have to check it as often so that the funding can be allocated to equipment in the plants with higher probability/consequence of failure,” explained Wang.
Abnormal Situation Management
Wang’s role is at times governed by the need to address any emergency as soon as it arises. “My day-to-day schedule is highly dependent upon task at hand. There are always long term items I work on, but as a large part of my day is dedicated to supporting manufacturing sites, my routine can be relatively fluid. If we have an emergency, I make it my number one priority,” he relayed. “For instance, in case there is an IOW exceedance, I’ll have to assess the risk, the time frame in which it has to be mitigated, and come up with a path forward for inspection if needed.”
Failure Analysis
Failure analysis, simply put, is the process of analyzing the failed material to determine how to avoid future damage or leaks. This includes diagnosing the cause of the failure and prescribing follow-up actions to address the cause. Improper design, choice of incorrect materials, abnormal operation conditions, bad maintenance practices, issues in inspection planning or execution are all potential causes for failures. Wang has seen failures which are caused by every one of the factors listed above. “The fact that there is a failure is always frustrating, but the process of solving a mystery can be quite fun and fulfilling,” he added.
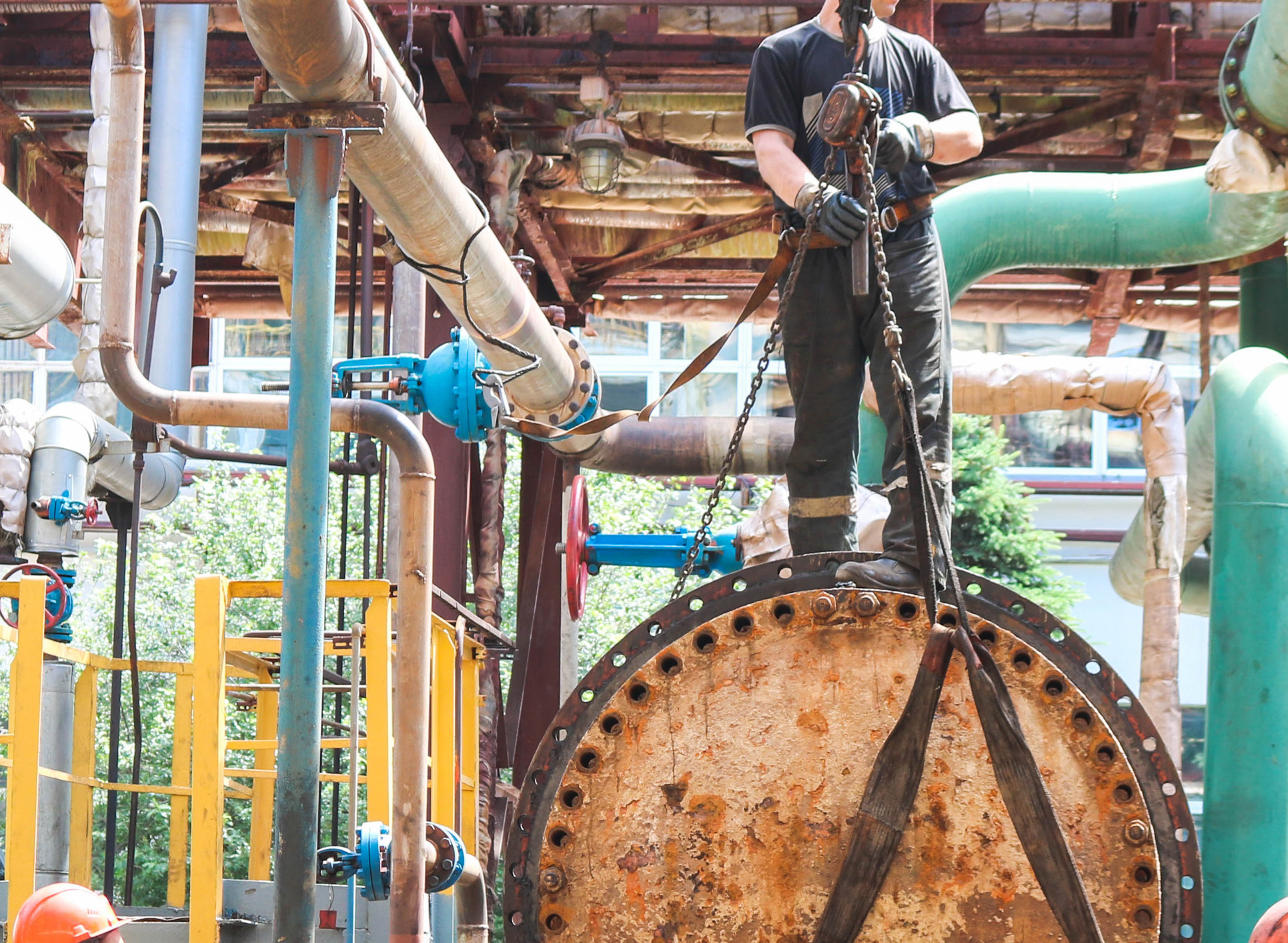
Looking Ahead
When asked about his stance on the future of stainless steel in an ever-changing environment, Wang noted that stainless steel offers good corrosion resistance and weldability in many applications. In a world where labor cost is constantly increasing, stainless steel may become even more popular due to its lower maintenance needs compared to carbon steels. “Stainless steels are not going anywhere any time soon. It is important for users in any industry to be aware of their advantages and limitations in each application so that material can be selected correctly per design.”
When asked about his advice to those entering the world of corrosion engineering, Wang simply said, “Be curious about technical knowledge and be willing to work with others. On one hand, technical knowledge provides the basis for good engineering judgement. On the other, good communication skills and the spirit of teamwork are essential for an engineer to succeed in their role,” he concluded.