Failure analysis is an essential tool for all industries. It is crucial to take the initiative to understand failure mechanisms in the workplace. Although senior personnel pass on information to juniors, there are frequent revisions to guidelines and improvements to processes which analysts can follow with ongoing education. Stainless Steel World Americas had the pleasure of speaking with Dr. Sudhakar Mahajanam, Failure Analyst, at Stress Engineering Services, to learn about his work in the field, and how he, with the assistance and collaboration of his team, receives and evaluates failures, while diagnosing the damage mechanisms and offering solutions.
By Sara Mathov
Getting Started
Dr. Mahajanam’s passion for the steel industry stems from his hometown in Jamshedpur, India, also known as The Steel City. After completing his bachelor’s degree in Metallurgical Engineering at the Indian Institute of Technology, he began his career with Tata Motors. A few years later, he accepted admission to The Ohio State University and went on to complete his Master’s Degree in Material Science and Engineering. He then enrolled in the Ph.D. program, where he had a chance to work on a multi-University industry project involving aircraft aluminum alloys and a newly developed coating system. “Once I received my Ph.D., I began working at Cessna Air-craft in Wichita, Kansas. This is where I picked up failure analysis,” stated Dr. Mahajanam. “While it is not something that is necessarily taught in schools, it is essential that analysts and industry professionals understand failure mechanisms in the workplace.”
Even though he enjoyed working on air-craft alloys, Dr. Mahajanam missed focusing on the research aspect of material science. To satisfy this desire, he took a position at the ConocoPhillips Research Center. “I became involved with the oil & gas industry where I began to further my research in materials utilized in upstream and downstream oil & gas production,” explained Dr. Mahajanam. “Although 90% of the material used is carbon steel, critical processes require the use of stainless steel and corrosion resistant alloys.”
A Day in the Life
In his current role, Dr. Mahajanam focuses on material testing and analysis. “My experience is somewhat unique because I have worked for an operator in the field and in a lab. Currently, I work in the lab, collaborating with technicians, technologists, and clients to generate data.”
A typical day for Dr. Mahajanam begins with reaching out to clients for potential projects. Connections with clients are achieved through attendance and presentations at large conferences, or with the assistance of the sales team. When project ideas are received, Dr. Mahajanam creates proposals that identify the project’s scope. The proposal then gets sent back to the client and once approved the lab receives the material that needs an assessment. Following the data generation and collection, reports are written and given to experts for review and approval. The document is then sent out to the client to make revisions, and to ensure that the intention of the company and the clients are the same. “The process I follow on a daily basis is directly involved with failure analysis,” he added.
Breaking Down Failure Analysis
According to the American Society for Metals (ASM) Handbook Volume 11, there are several steps followed to complete a failure analysis correctly. Broadly speaking, a failure investigation sequence involves two parts: the collection/examination stage (semi-interpretation) stage, and the analysis stage (final interpretation).
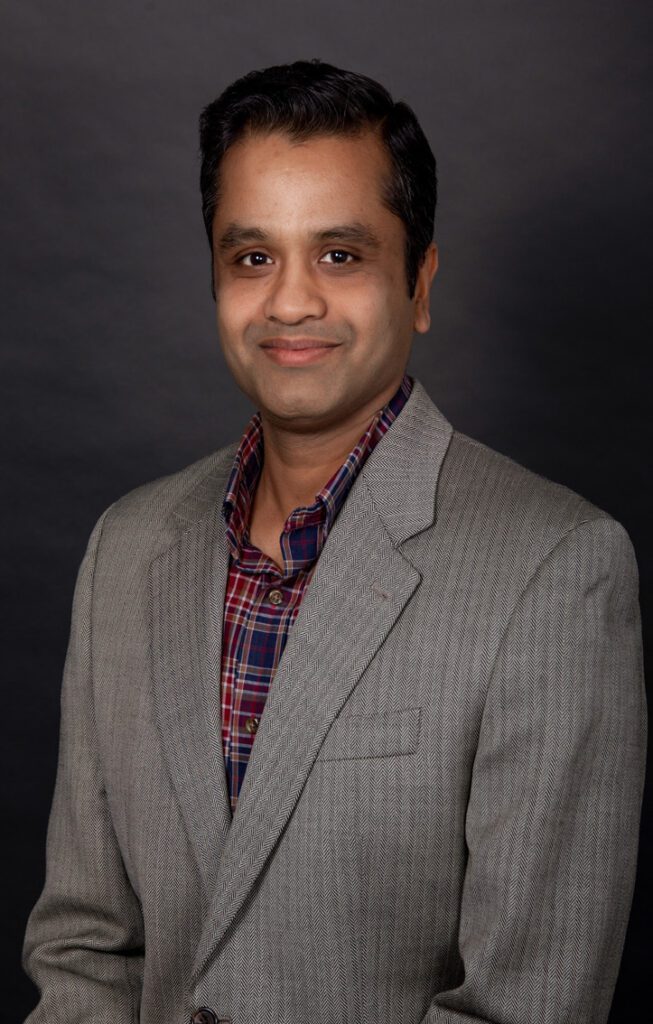
Semi-interpretive stage
This stage begins with data collection, which occurs in the field or a lab:
- The most critical part for this step is the visual and photographic documentation. This information usually becomes the key to solving issues, sometimes even before the failed component comes into the lab.
- When the part arrives to the lab, any contents or deposits inside are scraped out and preserved for chemical or microbiological examination.
- The sample is then subjected to non-destructive examination, mechanical property testing, macroscopic and microscopic examinations.
- Sample sections are identified for metallographic analysis.
Final interpretative stage
The second stage entails the analysis; the engineers work with technicians and field personnel to establish potential causes for the failure. For example, gas pipelines most likely experience failure when water condenses allowing it to react with contaminants such as carbon dioxide or hydrogen sulfide to cause corrosion. Pipelines carrying liquids, such as crude oil, can experience internal corrosion when water or solids drop out. The analysis stage involves the following:
- The metallographic sections are mounted in an epoxy mould, polished and etched to help document microstructural features and the damage mechanism. Carbon steel requires different etchants compared to those used for stainless steel.
- Chemical and microbiological analyses, as required.
- Occasionally, materials are tested under simulated service conditions to gather the information that may be otherwise not available.
- Once images and mechanical property databanks are collated, personnel begin creating a report and conclude relevant findings.

Current Projects
As an example of the benefit of failure analysis, Dr. Mahajanam discussed one of the most recent projects he worked on. “The client provided us two sets of 304 stainless steel pipes that had leaked during hydrostatic testing. The 12-inch diameter pipe ran both above and underground, and had not yet been placed in service. However, there were lapses in the project and standing water had been allowed to sit in the pipes for many months.”
For the above-ground pipe, the damage was observed on the body of the pipe, which is not a typical place for damage. The part of the pipe installed below ground had leaked at the welds, which is a common region for observing corrosion, damage, and failure. “After performing radiography to identify corrosion pits that had not broken through the wall and analyzing them, my team and I concluded that the leaks occurred as a result of internal microbiological corrosion. This damage is unique and can occur in 304 stainless steels. We utilized metallography, chemical analysis and microbiological testing to arrive at this conclusion.”
Microbiological damage had started on the inside surface of the pipe and made its way to the outside surface. Standing water inside the pipe in the month leading up to hydro testing had allowed the microbes to eat into the metal. “We suggested using a biocide or inhibitor in the pipe, to repel the bugs and “mothball” the pipes prior to hydrostatic testing,” says Dr. Mahajanam.
Corrosion Management: Prevention and Reduction
When looking at corrosion through the lens of metallurgy and material science, the focus is on the chemical reactions occurring on the metal leading to its oxidation. Within these chemical reactions, it is also important to consider the electrochemical reactions taking place as the metal begins to corrode. This in turn, helps determine corrosion rates which can be used to effectively monitor and control corrosion.
“When stainless steel was invented, its original intention was for use in applications that required material that would not stain or rust. As stainless steel does not corrode the way carbon steel would, it was implemented across several industries. On the other hand, carbon steel corrosion is predictable enough to allow maintenance personnel to follow a scheduled routine. Stainless steel does not offer this predictability,” said Dr. Mahajanam.
Stainless steels can undergo catastrophic cracking, which occurs without forewarning and can lead to disastrous consequences. Environmental factors often play a role in these cracking failures; such as chlorides in marine environments, or the harsher conditions observed in the refining sector and chemical plants.
Metals and alloys are typically manufactured by extracting them from their oxide ores. Metal oxidation or corrosion is inevitable; the job of operations personnel is to prevent or reduce this oxidization process. A large part of corrosion management is to ensure that corrosion occurs at a slower controllable rate, through the use of stainless steels and other corrosion-resistant alloys or controlling the service environment by adding chemicals or corrosion inhibitors to protect the asset’s integrity.
Corrosion is an interdisciplinary subject that involves chemistry/electrochemistry, electrical engineering, and material science. Corrosion management is vital to most industries, and the research behind it is critical, especially for future engineers.
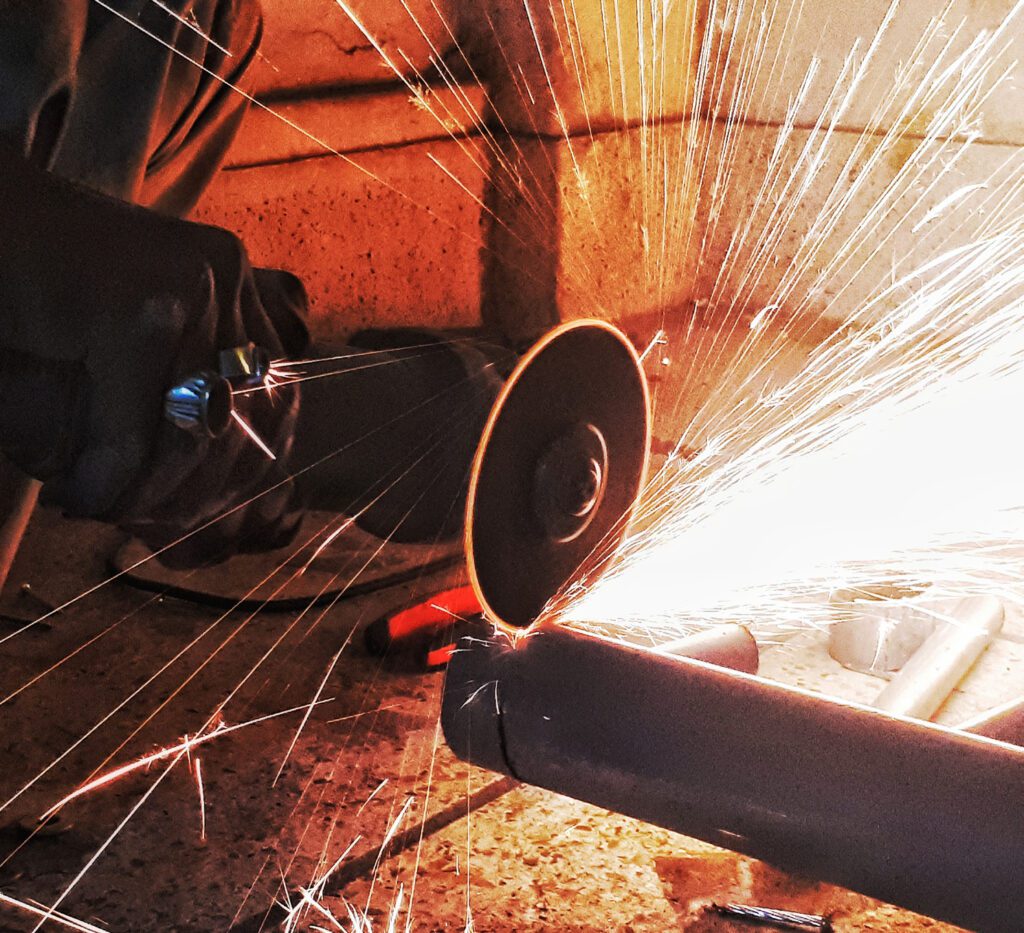
Looking Forward
“Corrosion management is a whole field of its own. There is metal that wants to corrode, and an environment that allows for corrosion. There is an anode, a cathode and an electrolyte, the three basic legs that form the basis for corrosion, and the challenge is trying to control one of the legs in order to prevent corrosion.”
Although he has a Ph.D., Dr. Mahajanam’s most favoured aspect of the role is the commitment to on-going learning. “It is a two-way process. You read more and you get more passionate about it; I think you need to have the passion for surviving in any industry. Stainless steel and its use in various applications are not going anywhere. There are still so many things to learn and discover given the vast number of alloys and materials,” stated Dr. Mahajanam. “An important part of this discipline is the number of core engineering jobs that will continue to become available. Corrosion is essentially extractive metallurgy in reverse, and I am truly excited to keep abreast of the innovations in corrosion prevention/protection,” he concluded.